「灿科盟」连接器生产厂家(浅谈连接器振动技术相关问题探讨)
本文章来源网络整理,字节5008个,阅读大约10分钟。
怎么知道在车辆振动下,怎么知道连接器有哪些因素影响整车故障?根据多年经验看,一台车有几百个连接器,其中约3000个单终端,连接器如果出现退化及其它故障时哪么有可能导致20%-50%的电气出现问题。
因此召回的案例也比比皆是,所以对于连接器,尤其在混动和纯电车辆下的高压连接器的可靠性就及其重要, 相比静态而言,车辆是移动的,所以就要着重考察在车辆全寿命及振动下的接触的可靠性等性能,基于此, 这篇文章我想主要写写连接器在车辆振动下的几个比较重要也是大家(无论是生产厂家还是使用厂家)应该重点关注的,高压互锁瞬断的问题、接触区域ECR变化以及微动磨损的影响程度、连接器怎么降低以及吸收来车辆的振动;
高压互锁瞬断的问题
按照高压电对人的危害来看,一般超过60V DC/ 30 V AC就会对人造成伤害,就必须进行电气安全保护,而无论是在混动还是纯电汽车,较高的电压系统带来了潜在的高压电击危险,一般电压上升会造成人体抵抗电流的内阻(阻抗)下降,会导致电流流入人体,严重的电流会造成伤害以及死亡,所以按照SAE J2344、ISO 6469和IEC 60664等国际标准对触摸安全连接的设计要求,引入高压互锁(HVIL)电路来保证高压连接断开的安全

整个回路中,如果有一点断开,BMS自动会发送报警,所以HVIL连接设计的好坏非常重要,在实际的应用中,这方面的出问题的比例非常高,怎么保证在严格的车辆振动情况下,HVIL接触依然是良好的,这个需要在设计时注意;高压连接器HVIL一般是由一个小的连接端子连接,一端采用短路设计,一端采用正负回路设计,连接器插合到位HVIL短路连接,未插合到位HVIL 开路状态,BMS通过检测HVIL回路的连接器情况来判定高压回路是否安全,是否需要整车下电,按照实际的经验来看,这个地方的接触不良现象较多,主要问题出在高压互锁端子的连接的可靠性,尤其需要满足车辆振动的严格要求;
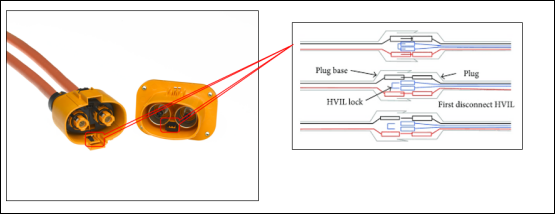
高压互锁其实就是一个信号端子,所以一般厂家设计其载流能力在5A以内,其功率很低,大多数厂家也都是沿用了传统汽车低压插件端子现成的设计,严格来说,这个无可厚非,毕竟电动汽车振动的标准和传统车辆对插件的标准也没有太大的差异,但是在传统车辆上,没有什么高压,没有单独的高压互锁概念,插件上也不用大小端子组合,插件的设计也充分考虑了端子的接触可靠性设计;但是在高压连接器里,它的设计重要性还是没有被单独对待进行设计,高压连接器一般功率更大,其工作时周边的腔室温度也较高,周边区域的环境温度也较高,这个与传统插件相比,这个互锁端子一样的设计,但是其工作环境还是有差异的,这种长期的工作环境会对基体材料的屈服老化变形产生重要的影响,使用寿命也会有所下降,尤其还要考虑高压下的尖峰问题(瞬间电源、瞬间电流)材料在长期的温度影响下,会发生老化变形,这种变形就会影响正压力下降,在初期会经常导致接触时好时坏等现象,这个矩形还是圆形端子关联不大,最终都是保证足够的正压力和接触力的;
高压连接器一般来说最低也要满足100次以上的插拔,对于power pin来说这个很容易,但是对于尺寸较小,厚度较薄的互锁端子来说,就需要特别注意这100次在加速老化后的接触表现,这个地方完全可以通过测试来体现出来,而且你除了考虑互锁端子本身结构的稳定性,你还必须考虑其腔体的尺寸在相关环境性能加速测试后的变化情况和温度性;
上面啰嗦了好多废话,总结一下,在85°环温下做测试,看互锁端子的材料变化情况,重点看其变形情况,最好在振动、温度、湿度同步的情况下测试,同时通过设计模拟和实验来测试和验证其屈服的临界点在哪里(不要迷信材料理论数据);另外需要关注其装配尺寸链在加速老化后是否还能保证如初,变化情况是否在可控范围内;
接触区域ECR变化以及微动磨损的影响程度
高压连接器的公母两端能够实现导通,是通过公端子和母端子接触,从端子的结构形状来说,常见的要矩形和圆形的,因篇幅关系,这个地方我们只以圆形结构为基础来阐述,同时我们的分析是基于公母端连接有弹性件的;我把我之前为企业培训写的资料摘抄了一部分,我觉得还是有必要做个简单是梳理,虽然之前的文章多少也写过;

端子的接触簧片
其性能直接影响了载流的传导的可靠性,振动下我们也是重点关注其接触电阻及微动磨损的情况,端子簧片主要包含了三个重要的功能,传输电力或者信号、提供端子正向力来建立和维持可分离的端子接触面、提供永久性端子接触界面的连接点。中间的弹性接触簧片的内阻决定了连接器的寿命(性能不失效的情况下插拨次数) 和失效的发生,一般来说有几个比较重要的设计指标需要在设计时需要考虑,材料、成型结构(几何形状)、电镀因素、插拔次数和圆周正向力等;
弹性接触的材料以铜或者铜合金居多,包括黄铜、磷铜、铍铜、纯铜、其它合金等,铍青铜因为其良好的导电率和屈服性能被广泛的运用到端子接触件设计种。
成型结构一般包含劈槽式结构、冠簧结构、线簧结构、双曲线笼簧结构等,目前双曲线笼簧结构其多次插拔后的稳定性比较高,通常在需要多次插拔的高压高流场景得到普遍应用,比如电动汽车充电口等,劈槽式结构因为其无法在插拔多次后保证良好的接触电阻,我们不做过多阐述,我们可以简单来比较一下冠簧、线簧、双曲线笼簧 三者之间的优缺点;
冠簧是一种非常普遍的弹性接触元件,我国在70年代初就已经在批量用于航天、工业自动控制、轨道交通等领域,按其形状还可以分为内冠簧和外冠簧,其经过很多的发展,其成本较为便宜,簧片一般采用铜材带料冲制而成,其结构形状有点像腰鼓,两头大中间小,中间腰的部分就是公端PIN针插入后接触的部分;

一般把冠簧装进母针的内孔中需要采用专门的收口工具(目前都是自动化作业以保证精度)装配后弹性材料回弹与内套配合,电流从公端的PIN针流入簧片中间腰鼓的接触区域(A)在中间区域流入簧片和内套接触区域(BC)实现传导,根据以往的经验来看,冠簧这种腰鼓式结构其稳定性不是很高,尤其是在车辆中,在传递高压高流又要兼具插拔时,车辆的不规则振动会造成簧片中间区域和PIN针接触不良,会造成微小的飞弧现象,时间长了会加速表面镀层磨损,会造成氧化,接触电阻会变大;另外在如图BC的区域其其接触力较弱,我们通过仿真软件分析发现电流流经此处时温升较高,冠簧是通过一种弹性材料变化收口装配至内槽中的,其有止位台阶(如果BC处),相当于是一种悬臂梁结构,长时间在车辆的振动环境下工作,容易造成材料屈服效应,造成失效;

线簧孔结构是大电流接线端子、接插件产品中高稳定,高可靠的接触元件,相比冠簧,其成本较高,一般只用于少部分场合,由数根金属丝绕内套,弯曲后,由两外套,从前后两端压入并紧固位一体。由于金属丝与内套轴线斜交有一个角度,形成单页双曲面结构,并形成一喉圆,其直径小于两端形成之孔径。当插针插入后,插针被各个金属丝所包容,由于各个金属丝都与插针接触,并受到拉力,所以电连接接触可靠,受力均匀 ;与冠簧的片式不同,线簧采用的是单根丝的传导,而铜丝的数量排布越多,传递的性能越好,成本和制程难度也越大,其和冠簧在与内套接触不稳定不同,其单根丝和PIN针之间的保持力是极具挑战的;
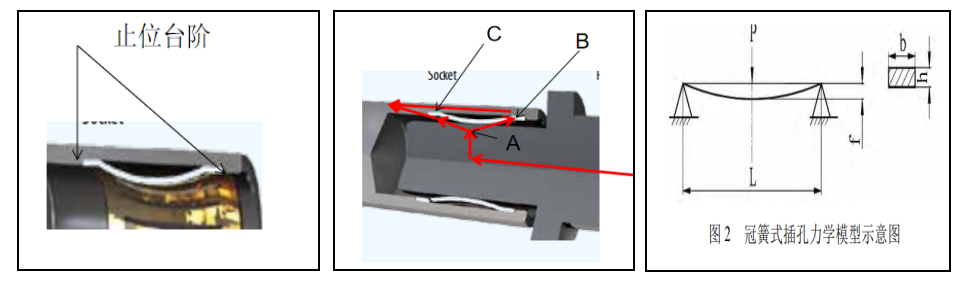
对于以上2种接触元件都存在一些问题点,所以对于电动汽车大功率,高压高电流的要求下,出现了双曲线笼式的结构,本质上来说,其是一种形状结构,接触类型可以是片式也可以是丝状,一般片式的居多,其接触面积及稳定性也较高,比较出名的是A厂家的Radsok专利技术
双曲面簧的设计是存在一定的难度的,双曲线是圆锥曲线的一种,即圆锥面和平面的交截线,双曲线有双曲线的函数,如下图一个焦点在X轴上,一个焦点在Y轴上,中心在原点,有2个标准的推导方程式;
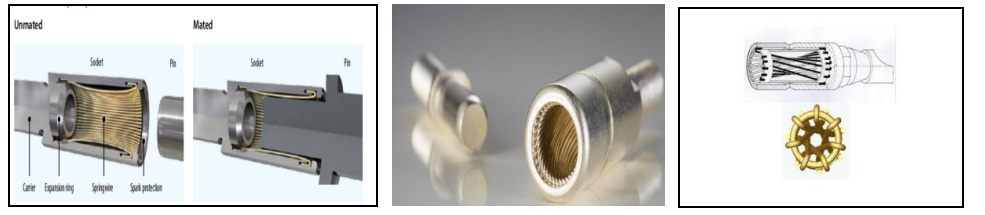
为什么要了解这个方程式呢?因为如果你想设计一个双曲线的结构笼簧,你就需要通过此公式和你的设计参数进行建模,通过模型带入数值,形成双曲线结构,最终在3D上形成3D的双曲线设计,再用3D的钣金功能进行展开,预留系数;在此不展开详细推导,感兴趣的朋友可以自行推导和设计。

当然,无论是矩形的片式端子还是圆形结构,端子的类型比较多,上面简单的说了几种圆形的,除此之外,类似劈槽结构的端子应用也比较多,比如如下是住友早期的AC充电口的端子,主要在容错角度的保证、加工工艺改善保证加工精度、以及产品在UL2251的10000次插拔后的稳定性 等方面做了改善和分析;
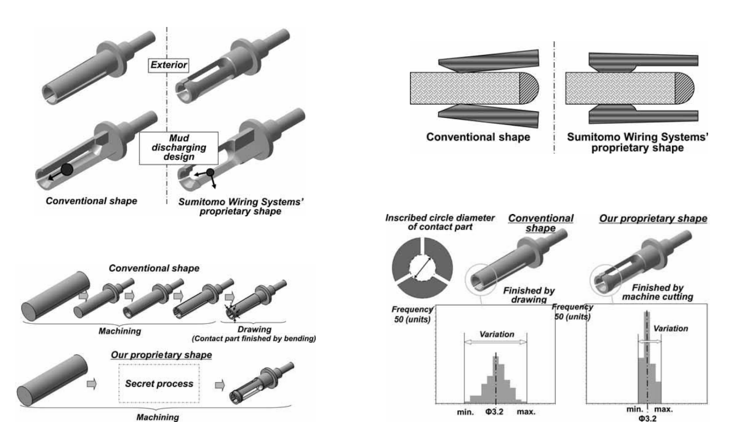
再比如ODU的 TURNTAC系列也是一种类似结构,该系列的也被广泛运用在大功率场合,比如北美特斯拉北美的AC充电contact,再比如Huber Suhner的大功率液冷充电口等
总结:结构类型是要基于你的设计要求来的,目前国内各家也都陆续有自己的专利,也在逐步打破早些年外资几乎垄断的局面;但是还是需要从产品的稳定性上去提高;
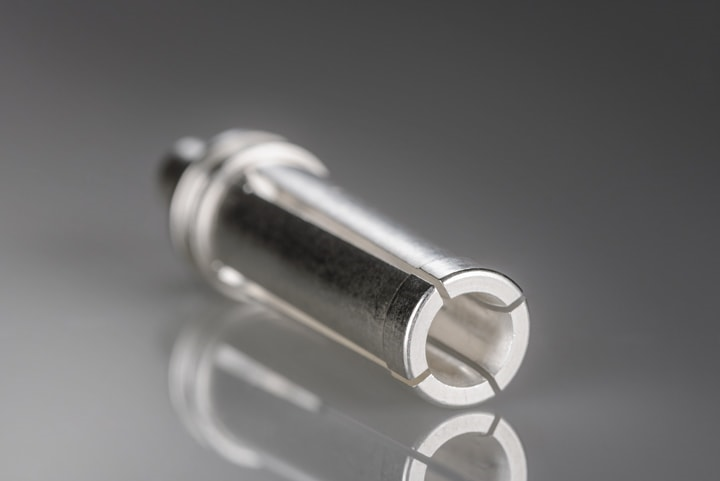
在确定端子的几何形状后,我们一般需要计算和测试样件的正向力,通过对材料的选择改善正向力,通过改善正向力来优化接触电阻的性能,首先我得知道什么是正向力,正向力的作用是什么,正向力(Normal Force)主要来自于两连接器插接时插座的端子梁因与插头配合产生的位移,由该位移产生的弹性恢复力就是端子正向力,又叫法向力,材料性能是决定端子正向力的基础,假如把端子近似视为一悬臂梁(梁的一端为固定支座,另一端为自由端)根据悬臂梁理论,可得到端子的正向力计算公式 ,其中D=梁位移量,E=材料弹性系数,W=端子宽度,T=端子厚度,L=端子长度,如果只是为了连接,其正向力可以很小的,但是如果为了保证接触的机械稳定性,那就需要平衡好正向力的大小了,正向力过大,直观的感受就是插拔力过大,而且在插拔过程种,在早期就会快速破坏你电阻的表层,不利于连接器的长期寿命,如果正向力过小,那接触电阻会非常的大,发热会比较严重,因为腐蚀物会进入接触面之间,通常来说正向力我们希望在满足性能的前提下越小越好,这个地方根据以往测试经验,我们需要注意的是正向力和接触电阻不是反比例关系,很多人认为是不是正向力越大,接触电阻越小呢?通过以往的测试实验结论,我们发现,在刚开始的时候接触电阻是下降很快的,但是后面插拔次数一定后,接触电阻就会趋于稳定,原因在于在该阶段接触件表面膜层不断破坏,表面膜层的破坏会导致接触电阻中的膜层电阻R会不断下降,所以接触电阻较低,但是在插拔一定次数以后,比如500次以后,随着插拔次数的增大,接触件表面镀层乃至基体不断磨损导致触表面粗糙,触点接触面积下降,同时经多次插拔后,簧片元件接触圈的弹性下降,插拔过程中接触正压力下降,导致接触电阻增大,我们需要注意的是在测试的时候需要考虑温度变化对材料的正向力的影响,这是非常重要的一点。一般来说,正向力都是需要借助仿真软件和不断的实验测试来优化得出的,对于设计人员需要对接触电阻的构成、正向力的计算有一定的了解;
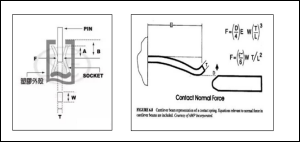
上面说了端子的结构形状等内容,除此之外,镀层也是影响ECR变化的重要因素,目前电动汽车高于连接器的镀层基本是镀银层居多,但是这个镀层它不是一层,一般来说 裸铜、镀铜、镀镍、镀银;之前要朋友问为什么不能镀锡,其实早期的连接器也要镀锡的,由于镀锡连接器由于其柔软性,成本低,ECR(Electrical contact resistance)相对较低,在传统汽车插件上应用比较广泛,但是锡是不能耐高温的,而且微观层面,镀锡层在振动下会产生微动磨损,在微动腐蚀过程中,微动磨损反复将新鲜金属暴露在大气中,导致接触界面上的 氧化和碎片堆积。这不断减少导电面积和电导率。因此,当振动被应用于镀锡连接器时,ECR将继续名义上和逐渐地随着时间的增加而增 加。但是与银涂层的连接器可以使微动腐蚀不那么显著;
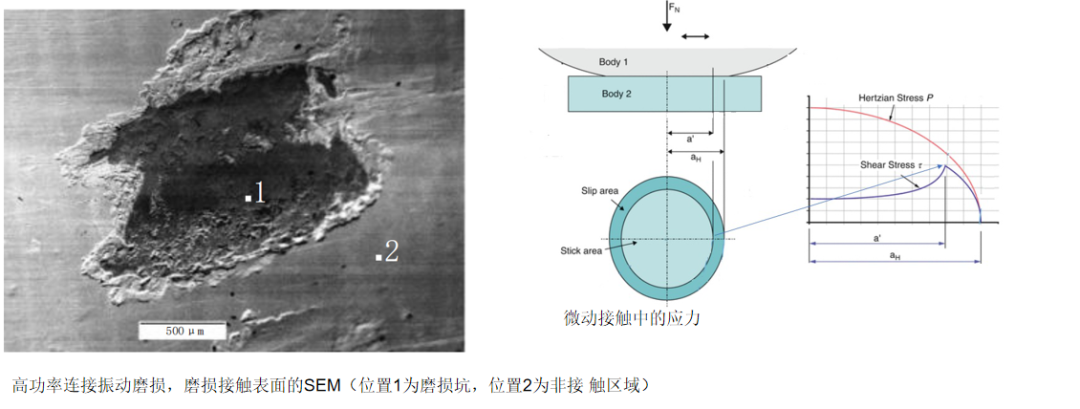
在大功率连接器里,微动磨损的影响是没有那么大的,当然如果镀银层被反复的插拔或者其它因素导致磨损直至露出基体,那磨损影响程度会比较大,最直观的就是其温度会很快上升,ECR的数值也会很大; 在小电流连接器里结果是完全不一样的;
连接器怎么降低以及吸收来车辆的振动
高压连接器在振动下,受影响的层面很多,上面我们聊了高压互锁在振动下的问题,以及端子的接触电阻和磨损腐蚀,下面我们聊聊连接器尾部出现线区域的影响;
电缆截面积越大,通过电缆长期施加给连接器的应力就会越大,这个应力会对尾部的防护可靠性以及尾部的压接区域的接触电阻造成比较直观的影响,一般来说为了降低和消除这个应力的影响,会通过2个层面来改善,我在这个地方增加了一个思考层面,就是3个层面:
连接器尾部出线固定
连接器固线器设计与运用
带吸收振动的阻尼防护结构设计
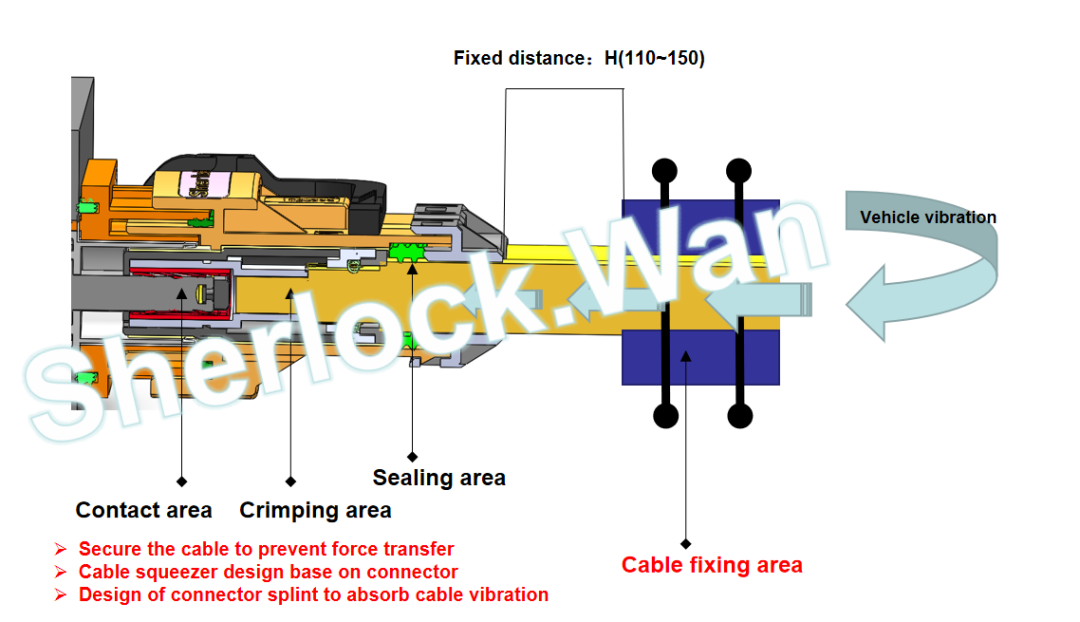
连接器尾部出线固定
这个出线固定方式很多,一般在商用车上会比较直观,可以通过夹板等方式,基本上是在尾部出线110~150之间进行固定,这个固定位置是比较有意思的,标准上我并未看见要明确的在布线上的要求距离,只在振动的相关标准上有所要求,但是根据经验,根据不同的线径规格,以及不同的安装部位,其传导应力会要所差异,其固定的位置也会有略微差异;如果要研究产品更微观的东西,感兴趣的厂家可以在这个地方不断的去仿真分析和试验来获取一些经验值
连接器固线器设计与运用
这是从连接器层面去考量怎么最大程度提高连接器抗振性,有些做法是增加连接器尾部尾夹延伸距离,还有的企业是在尾部增加单独的固线器,有对卡式的,也有螺钉固定式的,其实这种方式在工业以及轨交行业里设计很常见,也是变相的增加了一个固定点,不断的降低振动的传递力,比如如下是Aptiv的一个专利固线器设计结构;
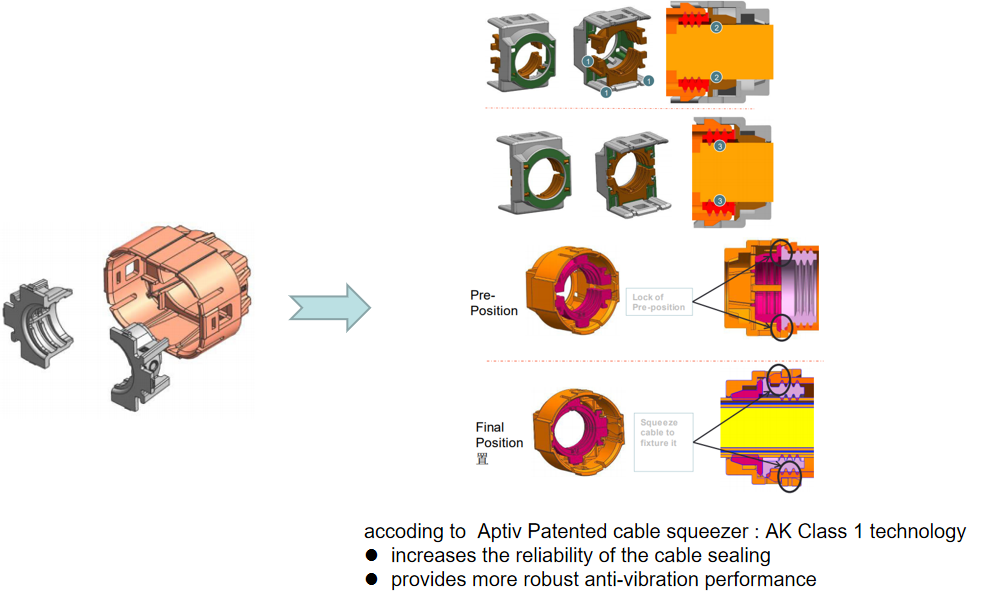
带吸收振动的阻尼防护结构设计
比亚迪的同事说,在未来连接器应该承担更多的振动带来的力,这个思路我也比较认同,我觉得连接器在尾部的结构,后面可以在考虑最大程度的设计一种同时可以防护,同时又可以吸收振动的弹性结构,根据我在各个现场看到的问题,这个地方是一个非常值得深入去改善的地方,也非常希望看见国内同行能有好的设计出现;